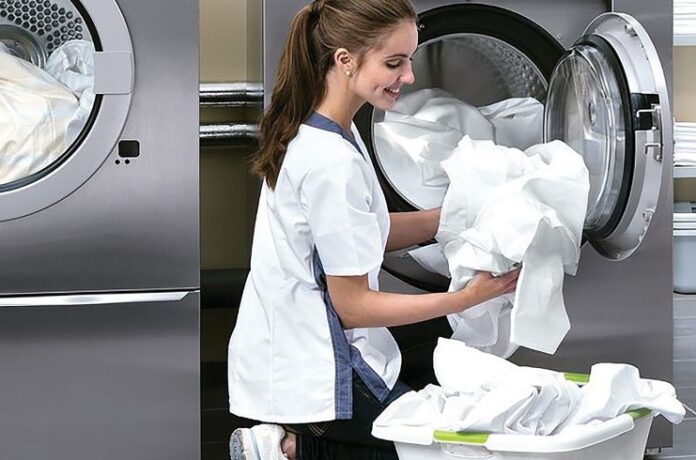
The laundry room is a significant hub of housekeeping operations, and extremely environment friendly washers and dryers can save labor time and prices, whereas supporting sustainability initiatives. Based in Germany in 1899, Miele, Inc. is among the world’s most venerable producers of economic laundry gear, with 125 years of expertise within the European market and about 41 years within the U.S. market by way of Princeton, New Jersey-based Miele USA. Along with that formidable historical past, the corporate stays on the vanguard of laundry gear know-how, commonly conducting R&D into options and options that may make housekeeping groups simpler on this indispensable space of operations.
Within the following dialogue with LODGING, Paulo Rocha, Miele’s head of gross sales | HCS Enterprise Unit | NAM Area, explains the current evolution of those machines and gives suggestions for resort operators seeking to procure the very best gear for his or her wants.
LODGING: How have washer applications turn into extra refined?
Paulo Rocha: The applications that the machine comes with are essential. Within the U.S. market, the producers or distribution corporations normally simply promote the machines, and the chemical corporations are those that construct the applications in line with the textiles the machine wants to scrub. We at Miele know the textiles—whether or not it’s polyester, silk, wool, and so forth.—and so our machines already include this system packages. And since our machines are freely programmable, we are able to truly tweak the applications to supply a good higher service. We now have a touchscreen answer the place you will discover the manufacturing unit program that may match what you must wash, or we are able to tailor the applications: They are going to have the names that the client needs them to have, keyed to the kind of merchandise to be washed, for instance.
LM: Can the touchscreens accommodate multilingual employees?
PR: All of the Miele machines have a button to pick your language, and now we have greater than 30 languages obtainable. We provide employees coaching in a number of languages as nicely.
LM: What options can be of curiosity to resorts with restricted laundry room house?
PR: With the smaller fashions, now we have stacked choices. So, as a substitute of getting a wash and a dryer aspect by aspect, you’ll be able to stack them. And for each three or 4 washers, you simply want two dryers as a result of when our washers do the ultimate extraction, the textiles come out nearly dry. So, your drying occasions are 15-20 minutes tops versus 30, 40, or 50 minutes, for instance.
LM: What sort of know-how permits Miele washers to output practically dry materials on the finish of their cycles?
PR: Our patented honeycomb drum, which is in-built a approach that minimizes the damage and tear on clothes or textiles. With an everyday drum, each time that it goes to an extraction, it’ll break the fibers on the microscopic degree and finally cut back the lifespan of that textile by a half or extra. With our high-extraction drum, the textile will final three to 5 occasions longer in comparison with different drums. And because it’s not tearing the textiles on the microscopic degree, there may be 90 % much less lint when it goes to the dryer.
LM: Can a resort operator decide what number of washers they’ll want primarily based on the variety of rooms within the property?
PR: We now have an Excel sheet calculator for that. However it all is determined by how a lot the resort is definitely washing in-house. Most resorts use a third-party firm for many of the washing and solely do some objects in-house, just like the towels. A 150-200 room resort utilizing that process would in all probability solely want two washers and two dryers that deal with about 55 kilos per load of laundry.
LM: How do your machines assist sustainability objectives?
PR: We’re acutely aware about saving power and water, so all our washers, while you examine with different manufacturers, use 25 % to 30 % much less water and fewer power.
LM: What pointers would you counsel for resort operators seeking to associate with a laundry gear vendor?
PR: For my part, what issues for the hospitality enterprise is just not the machine’s value, however fairly how a lot it will possibly produce and the way a lot cash it will possibly save. The extra it saves throughout operation, the extra that preliminary value will probably be diluted. Labor could be very costly and never too straightforward to search out, so hoteliers must have their employees do extra in much less time, however with high quality outcomes. The second consideration can be, how dependable are the seller’s machines? Do they break down continuously or are they ready, like our machines, to work 30,000 hours, which implies 15-20 years of operation? And the third consideration can be, what’s the assist you can get? We now have our personal technicians that may assist our distribution companions which might be unfold throughout the nation. We prepare these companions to be nearly as good as our personal technicians.
Distant Upkeep: A Wi-fi Answer for Proactive Washer Care
Distant monitoring and upkeep is a trending characteristic amongst various kinds of resort gear, together with washers. Vendor employees use the system to examine the machine’s efficiency in actual time and determine any issues earlier than they escalate, versus a technician inspecting the machine in individual and explaining any vital repairs to the resort operator.
Miele, Inc. lately launched a wi-fi upkeep system for its business machines in Europe that may even be obtainable in the USA quickly. Referred to as Miele MOVE, the platform connects to washers by way of WiFi, enabling representatives to textual content the client about any upkeep wants they detect, in addition to service dates to handle these points. Paulo Rocha, head of gross sales | HCS Enterprise Unit | NAM Area, Miele, Inc., defined that this know-how can make sure the machine’s uninterrupted operation. “Usually, they solely name the service individuals when the machine is down. This software helps us advise the client if there’ll ultimately be injury to the machine if preventative upkeep is just not carried out inside a sure timeframe,” he mentioned.
In fact, a distant upkeep system and technician visits aren’t any alternative for workers coaching on correct machine care. “Consumer coaching to me is essential,” mentioned Rocha. “The washer shouldn’t be one thing that simply reveals up within the house and employees should work out the best way to use and keep it by themselves. So, we prepare customers on fundamental practices reminiscent of cleansing the filters day by day, checking the drainage system for clogs, and so forth. Additionally essential is holding data on the upkeep of every machine, which makes it simpler for service individuals once they arrive.”